We recognise activities at our operated assets can impact the health of our people and the communities where we operate.
Our ambition
Our approach and position
Mandatory requirements to manage and protect the health and wellbeing of our employees and contractors are set out in the Health Global Standard and our mandatory minimum performance requirements for risk management, as well as local regulatory requirements, standards and procedures.
-
Governance and oversight
For information on the role of the BHP Board in overseeing our approach to and delivery on sustainability refer to the Sustainability approach webpage.
Health hazards identified in our workplaces include exposure to musculoskeletal stressors, noise, coal mine dust, respirable crystalline silica, diesel particulate matter (DPM) and psychosocial hazards. We manage our exposures to potentially harmful substances and agents with internally specified occupational exposure limits (OELs) and by implementing a program of preventative health measures and wellbeing support.
For our occupational exposures, our process to set OELs involves periodic monitoring and evaluation of scientific literature, benchmarking against peers and engagement with regulators and OEL-setting agencies. Our approach to monitoring and reviewing our internal OELs is designed to ensure they continue to be aligned with or are stricter than applicable regulated health limits. We implement a range of exposure reduction activities designed to reduce exposures to harmful substances to as low as reasonably practicable.
We conduct periodic medical surveillance to detect signs of potential occupational illness at an early stage and assist our people through the management of illness that is a result of exposure to certain harmful substances and agents at our workplaces. Our medical surveillance program is based on local regulatory requirements and evidence-based industry best practice. The effectiveness of our exposure controls is regularly reviewed and subject to periodic audit to verify the controls are implemented and operating as designed.
The Health Global Standard is based on internationally accepted practice with requirements to identify occupational exposures with the potential to cause harm; assess the risk posed by those exposures; implement exposure controls; and where exposure cannot be immediately reduced to an acceptable level, provide personal protective equipment (PPE) and undertake health surveillance. -
Engagement
In line with Our Charter and our culture of care, we undertake activities to enhance the physical and mental wellbeing of our employees and contractors. This includes the provision of preventative health measures as appropriate for the location, such as vaccinations, gym facilities, onsite physiotherapy, healthy food alternatives at our worker village accommodation and a range of mental health resources including our Employee Assistance Program (EAP) and peer support programs.
A range of targeted health programs, such as sleep and heat management are made available at many of our operated assets where there are relevant workplace issues. Workers at remote sites are provided with emergency medical care and primary health care through onsite medical facilities, with telehealth consultations available. These services are provided by qualified individuals, including paramedics, occupational health nurses and medical practitioners, as appropriate, depending on the location. In most of our remote operations, these services are accessible during and after working hours.
We continue to monitor emerging health issues and trends through our membership of industry and professional associations, informal benchmarking, industry collaboration, networking and participation in national and international conferences. We also monitor information from scientific journals and occupational health regulatory setting and advisory agencies. -
Occupational illness
The reported occurrence of occupational illness for employees in FY2025 was 319, or 4.64 per million hours worked. This represented a 14 per cent increase compared with FY2024. For our contractor workforce, the reported occupational illness in FY2025 was 234, or 1.94 per million hours worked, a 8 per cent increase from FY2024.
Employee occupational illness
Footnotes:
1. Prior year data (FY2021 to FY2023) excludes former OZ Minerals Australian assets (acquired 2 May 2023), which is included for FY2024 and FY2025. Prior year data (FY2021 to FY2023) also excludes (entirely) divested operations as follows: BHP Mitsui Coal (divested on 3 May 2022) and BHP’s oil and gas portfolio (merger with Woodside completed on 1 June 2022).
2. FY2024 data has been adjusted and restated to exclude BHP Mitsubishi Alliance (BMA)’s Daunia and Blackwater mines (divested on 2 April 2024).
3. Occupational illnesses excludes COVID-19 related data.
4. Due to the lag nature of incident reporting and subsequent verification, final results may vary post reporting. Refer to the BHP ESG Standards and Databook 2025 for restatements made to prior year injury and illness data.Contractor occupational illness
Footnotes:
1. Prior year data (FY2021 to FY2023) excludes former OZ Minerals Australian assets (acquired 2 May 2023), which is included for FY2024 and FY2025. Prior year data (FY2021 to FY2023) also excludes (entirely) divested operations as follows: BHP Mitsui Coal (divested on 3 May 2022) and BHP’s oil and gas portfolio (merger with Woodside completed on 1 June 2022).
2. FY2024 data has been adjusted and restated to exclude BMA’s Daunia and Blackwater mines (divested on 2 April 2024).
3. Occupational illnesses excludes COVID-19 related data.
4. Due to the lag nature of incident reporting and subsequent verification, final results may vary post reporting. Refer to the BHP ESG Standards and Databook 2025 for restatements made to prior year injury and illness data.
5. Due to regulatory regimes and limited access to data, we do not have full oversight of the incidence of contractor noise-induced hearing loss (NIHL) cases.Musculoskeletal illness was the predominant occupational illness for employees and contractors, representing 64 per cent of our workforce illnesses in FY2025. This includes damage to bones, joints, ligaments, tendons and soft tissues caused by repetitive heavy work, muscular strain or maintaining poor postures for extended periods of time.
Noise-induced hearing loss represented 10 per cent of occupational illnesses in FY2025. Employees and contractors exposed to noise levels above the defined workplace exposure limits in our Health Global Standard participate in hearing conservation programs, which include a periodic hearing test and hearing protection fit testing. We have implemented established design recommendations that seek to eliminate or reduce high or prolonged noise exposures as far as reasonably practicable by focusing on the noise source.Occupational exposures
BHP seeks to reduce occupational exposures to as low as reasonably practicable. Where there is a potential for our employees and contractors to be exposed to chemical and physical hazards, we implement controls designed to prevent, minimise and/or mitigate the likelihood and severity of potential associated health impacts. These controls may include the use of PPE until appropriate, higher order controls have been identified, implemented and verified to consistently reduce exposure below OELs.
Our OELs are set by reference to the level of permissible exposure for a length of time to a chemical or physical hazard that is assessed as not likely to affect the health of a worker, according to scientific evidence and regulatory requirements.
Exposure data is presented without considering the use of PPE, which is required to be worn as outlined in our Health Global Standard to reduce exposure.
In FY2025, we recorded an overall 13 per cent decrease in the number of employees and contractors potentially exposed to DPM and respirable crystalline silica (RCS) compared to FY2024. This included a 73 per cent decrease in the number of employees and contractors with potential exposure to DPM and a 35 per cent increase in the number of employees and contractors potentially exposed to RCS. The increase in potential RCS exposures is primarily due to the inclusion of the recently acquired Copper South Australia operations within BHP reporting. Opportunities to improve control frameworks and hygiene practices at Prominent Hill and Carrapateena operations have been identified. We are pursuing both short- and long-term initiatives to reduce potential exposures, such as improvements to underground ventilation systems.
We continue to implement exposure reduction plans for RCS at our operated assets with a focus on engineering solutions to sustainably control exposure. At BMA, dust extraction systems have been implemented to remove dust build-up in mining haul truck electrical cabinets. Wet cleaning methods and vacuum systems have been implemented at New South Wales Energy Coal to reduce potential exposure for cleaning and maintenance teams. At Western Australia Iron Ore, portable extraction ventilation and dust suppression is in place for drilling personnel.
From December 2026, new lower exposure limits based on Australian legislation are expected to be adopted throughout Australia. We will continue to monitor and assess the impact of OEL changes and implement appropriate action as required.
We are committed to having no fatalities and life-threatening illness events connected with occupational exposures at BHP, and managing any risks of life-altering injuries and illnesses. Due to the latency between initial exposure and diagnosis of disease for our most material airborne contaminant exposures, we must continue to reduce potential exposure and monitor the effectiveness of controls where reduction of potential exposure is not reasonably practicable.Exposure reduction trend over time1,2,3,4
Footnotes:
1. Prior year data (FY2021 to FY2023) excludes former OZ Minerals Australian assets (acquired 2 May 2023), which is included for FY2024 and FY2025. Prior year data (FY2021 to FY2023) also excludes (entirely) divested operations as follows: BHP Mitsui Coal (divested on 3 May 2022) and BHP’s oil and gas portfolio (merger with Woodside completed on 1 June 2022).
2. Occupational exposure data is presented without considering protection from the use of PPE (where required as outlined in the Health Global Standard). The data excludes Projects.
3. As of FY2021, the OEL limit for Coal was reduced to 1.5 mg/m3 compared to 2.0mg/m3 in previous years.
4. As of January 2024, the OEL for welding fumes within Australia was reduced to 1mg/m3 compared to 5mg/m3 in previous years.Managing heat stress
Heat stress contributed to 4 per cent of our reported occupational illnesses in FY2025. Elevated temperatures and strenuous activity place some of our workforce at increased risk of heat illness. High-risk work groups are identified, and controls are in place to manage heat stress. Hydration testing is in place at operations with high heat risk. Our operated assets exposed to extreme climatic conditions have additional support to help prevent heat-related illness.
Coal mine dust lung disease
We have controls in place at all our relevant operated assets with the goal of ensuring no employees or contractors are exposed to respirable coal mine dust (CMD) above the OEL. We continue to identify and progress projects, such as enhancing our real-time dust monitoring, to identify when the working environment may present a hazard, allowing us to address the issue. We prioritise controls that are most effective, such as dust suppression and dust extraction engineering controls, to eliminate or reduce potential exposures as far as reasonably practicable instead of relying on controls that are less effective, such as respiratory protection. We have observed consistent control of CMD exposures with no employees or contractors potentially exposed to CMD above the OEL since FY2021.
In FY2025, 21 cases of coal mine dust lung disease (CMDLD)1 were reported to the Workers' Compensation Regulatory Services.2 There was one claim accepted for a current BHP employee. For cases involving current employees, we offer counselling, medical support and redeployment options where relevant. Former employees may be eligible for workers’ compensation insurance and their associated care is managed externally to BHP.Footnotes
1. CMDLD is the name given to the lung diseases related to exposure to coal mine dust and includes coal workers’ pneumoconiosis, silicosis, mixed dust pneumoconiosis and chronic obstructive pulmonary disease.
2. Cases reported to Workers' Compensation Regulatory Services are not an indication that the CMDLD was related to work. BHP evaluates each case for work-relatedness and, where identified, the case will be included in occupational illness reporting.Physical and mental health
The physical and psychological health and wellbeing of our workforce is paramount. We continue to enhance the inclusivity and future-readiness of our employees and contractors. We engage with initiatives such as ‘Minding Mining Minds’, which aims to develop tools and evidence-based models to build capability and share these learnings across industry, along with the Building Safe and Respectful Workplaces (BSRW) program, which strives to eliminate disrespectful behaviour in the resources industry, including sexual harassment, bullying and racism. In FY2025, we included the BSRW education into our global onboarding training and we refreshed Our Code of Conduct training.
The BHP Global Wellbeing Committee brings together asset and corporate office Wellness Committees into a global collaborative forum that shares experiences and implements improvements. The aim is to build mental health literacy, increase awareness and benefit overall physical and mental wellbeing of our workforce. In FY2025, we had strong participation in global health campaigns such as Women Can, BHP Mental Health Month, RUOK? day and Movember.
The new EAP provider also offers a broader range of holistic support services, including nutritional, career, financial and legal counselling. This has enabled us to introduce specialist helplines, such as for domestic violence, Indigenous employee support and LGBT+ hotlines.
BHP offers support for employees affected by family and domestic violence. BHP’s Family and Domestic Violence Support Policy aims to provide employees with support for their health, safety, wellbeing and independence if they are experiencing family and domestic violence.
Risk
When a health risk has the potential to impact the health or wellbeing of our people, we apply BHP’s Risk Framework to identify, assess and manage the risk. For more information on risk, refer to the BHP Annual Report 2025.
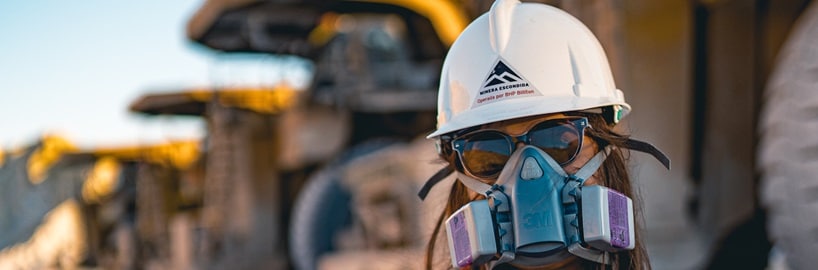
One Health – An Online Tool for Managing Health Surveillance Programs
At BHP, health surveillance is used as a proactive approach to help ensure the health and safety of our workers. It involves using medical tests to monitor the health status of our workers, enabling early identification of relevant health changes.
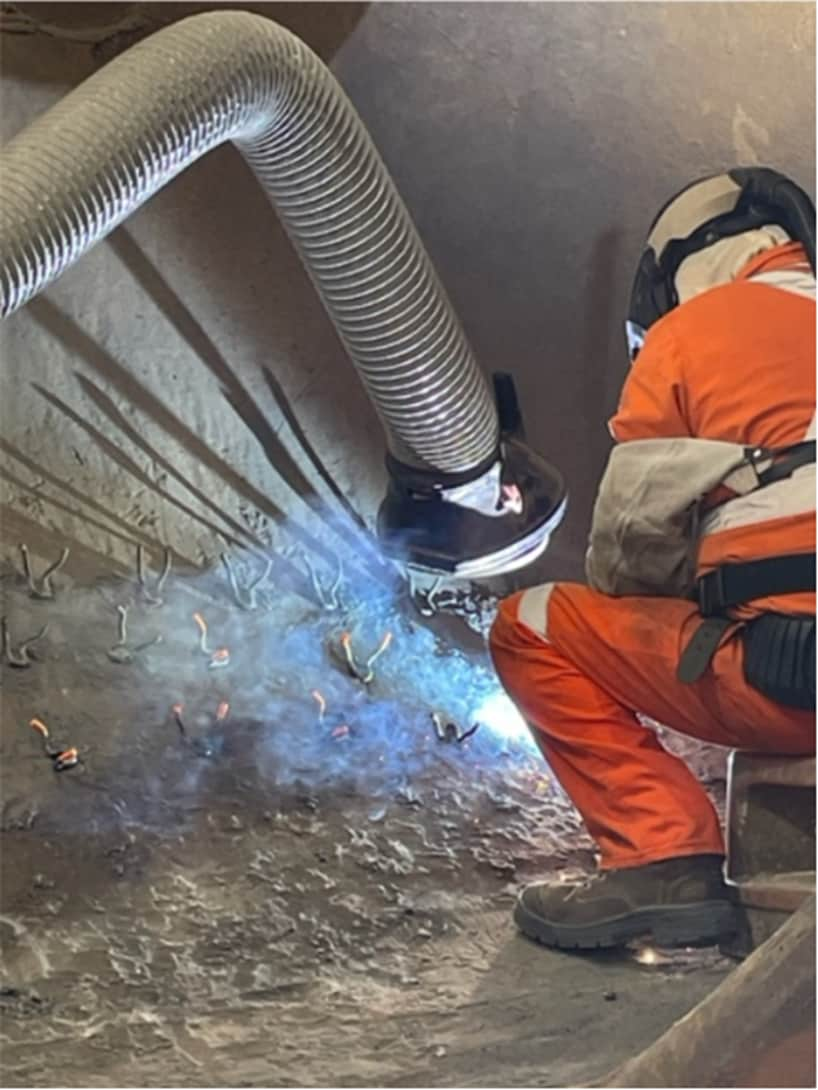
Reducing welding fume exposure at Olympic Dam
Our Smelter Maintenance team began collaborating with our Occupational Hygiene team in 2021 to implement improved controls with the aim of achieving significant welding fume exposure reductions.
Sustainability case studies, organisational boundary, definitions and disclaimers, and downloads
Prior year versions of some of the listed documents are available on the Past reports page.-
BHP Annual Report 2025
pdf
17068205
-
Sustainability reporting organisational boundary, definitions and disclaimers
pdf
170075
-
Límite organizativo de los informes de sostenibilidad, definiciones y descargos de responsabilidad
pdf
234993
-
BHP ESG Standards and Databook 2025
xlsx
2539492
-
BHP Group Modern Slavery Statement 2025
pdf
7308735
-
BHP GHG Emissions Calculation Methodology 2025
pdf
1124687
-
BHP Climate Transition Action Plan 2024, subject to updates of certain aspects of our assumptions and plans in the BHP Annual Report 2025, Operating and Financial Review 9.8 – Climate change
pdf
8480121
-
Global Industry Standard on Tailings Management - Public Disclosure 2025
pdf
25537144
-
Tailings Storage Facility Policy Statement 2023
pdf
73457
-
Information for social investment partners
pdf
26113
-
Case studies