05 November 2020
This episode is the second in our pathways to decarbonisation series. It is also the first of two articles on the global steel sector. Here, we focus on the technology options the steel industry has at its disposal to address the decarbonisation challenge.
Episode one: power, is available here.
Steel is the backbone of the modern built environment. It is the world’s second largest commodity value chain after crude oil. It underpins daily life. And as climate change and the energy transition unfold, steel will emerge as a building block of global mitigation and decarbonisation efforts across all key sectors.
The steel industry itself has a major role to play in reducing its own emissions, which are around 7-10% of global greenhouse emissions.1 The success of the steel industry in reducing these will play a crucial part in the global challenge to decarbonise economic activity without any trade-off in terms of future living standards.
We stand ready to partner with our customers on this journey. As a leading supplier of steelmaking raw materials, BHP has taken an industry leading position by outlining specific goals and actions to address our downstream Scope 3 emissions. We approach this challenge with both deep technical knowledge and multi-decadal relationships with our customers across the major steelmaking regions.
Firstly, let us consider how steel is manufactured today.
Steel is manufactured by two main process routes (Figure 1):
- the integrated steelmaking process featuring the blast furnace/basic oxygen furnace (BF/BOF), where iron ore is the major source of iron units; and
- electric steelmaking based on the electric arc furnace (EAF), where steel scrap or direct reduced iron (DRI) are the major iron feedstock materials.
Figure 1: major steelmaking process routes.
As the dominant route, integrated steelmaking represents 72% of global steel production. This varies by region, with factors such as scrap availability and fuel costs playing important roles in determining BF/BOF competitiveness versus the EAF process. In regions where scrap and/or natural gas are available at affordable prices, EAF steelmaking tends to have a higher share of steel production, e.g. in North America or the Middle East and North Africa (Table 1).2
Table 1: snapshot of global steelmaking as of 2019 (Sources: worldsteel, BHP estimates).
Let’s explore these processes in more detail.
In the integrated steelmaking route, iron ore containing ferrous oxides is converted to metallic iron inside the blast furnace via a chemical process called ‘reduction’. Coal in the form of metallurgical coal and pulverised coal act as the active agents or ‘reductants’ that strip away oxygen from the iron ore to yield metallic iron. With temperatures inside the blast furnace reaching over 2000°C, the resulting metallic iron melts and the liquid hot metal is ‘cast’ from the furnace and transported to the basic oxygen furnace. Here, the high-carbon hot metal is refined using oxygen and fluxes (e.g. limestone, dolomite), forming a slag that removes unwanted impurities including carbon, silicon and phosphorus to yield liquid steel.
Through advancements in technology and process control, a modern blast furnace can operate continuously for at least half a century, undergoing a number of major overhauls or ‘relines’ every 15-20 years to maintain an efficient operation.
Faced with a choice between retiring a blast furnace early to switch to more carbon efficient technology or extracting a normal lifetime from the existing facility via periodic relining, the industry is strongly incentivised to choose the latter under current policy parameters.
The arithmetic is clear. The capital cost for a typical 4.0 Mt per annum integrated steelmaking facility is in the order of US$4 billion. That compares to the relatively modest cost of relining a blast furnace, which we estimate are between US$50 million and US$200 million, depending on the jurisdiction. For regions with a young blast furnace fleet such as China or India, we see these steel producers running their furnaces for another 30-40 years. For North America, where the average blast furnace age is approaching 50 years (i.e. some will be considerably older), a decision to move away from the integrated steelmaking process at scale is likely to come considerably sooner. That said, we are observing customers in developed regions such as Europe investing in technologies to extend the life of their blast furnace assets by further optimising their carbon efficiency.
Steel is already one of the most recycled materials in the world, and is therefore a cornerstone of the circular economy.
Electric steelmaking differs from the integrated route in that the EAF feedstock, steel scrap or DRI, is already “reduced” and in its metallic form. The metallic charge only needs to be melted to convert the scrap/DRI into liquid steel.
In the DRI process, iron ore in the form of lump or pellets is reduced to metallic iron in the solid state unlike in the BF where the material is melted. Today, about 100 Mt of DRI is produced globally each year, with the majority of that using reformed natural gas (essentially splitting natural gas into hydrogen and carbon monoxide) to strip away the oxygen from the iron ore. DRI, or its compacted form hot briquetted iron (HBI), is a versatile feedstock that can be utilised in the BF or BOF to boost productivity, lower fuel rates or replace scrap in the EAF to dilute impurities from steel scrap to enable the production of higher quality end products. In some plants, EAFs melt 100% DRI where scrap is not available or unduly expensive.
Steel produced from EAFs using 100% scrap tend to lower quality, since impurities such as copper present in recycled steel scrap and that cannot be removed in the steelmaking process impacts the steel’s mechanical properties. For that reason, production of more demanding steel grades, such as those used in auto sheets or pipes, requires the addition of high-quality DRI or pig iron to the EAF process to dilute the impurities present in the steel scrap.
The emission footprint of the two major steelmaking processes differ substantially. On average, the integrated steel making process releases around two tonnes of CO2 per tonne of steel product (2.0 t CO2/t steel) in both direct and indirect emissions (i.e. from off-site power sources). Emissions from DRI vary with the source of fuel, with coal-based DRI in India, producing around 2.4 t CO2/t steel and natural gas-based DRI producing around 1.4 t CO2/t steel. Of all the current commercially available technologies, scrap based EAF steel making is the greenest with emissions of around 0.4 t CO2/t steel on average, depending upon the CO2 emission intensity of the electricity used. Based on the split of production route and region, the global steel CO2 emission intensity is estimated at 1.7 t CO2/t steel (Figure 2).
Figure 2: typical carbon emissions intensity by process.
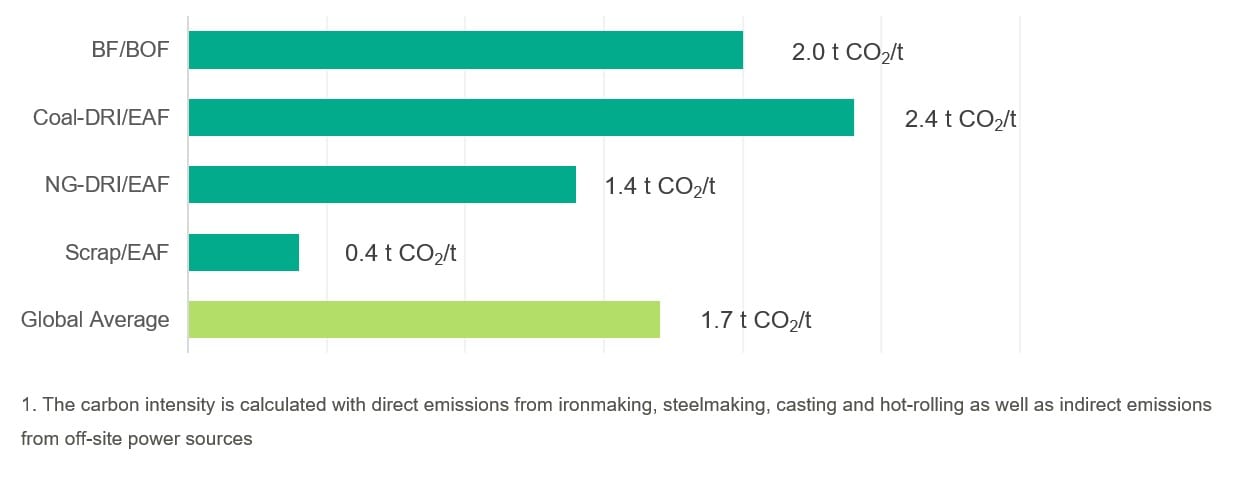
So why don’t steelmakers simply increase their share of EAF steelmaking to address the decarbonisation challenge?
The simple answer to this is that scrap and DRI are in finite supply: and that supply falls far short of global needs. We anticipate that all major regions will increase their scrap usage over time, but the pace of change will be determined, principally, by scrap availability. That in turn depends largely on the availability of end-of-life/obsolete steel stock. This is something we study in great depth. Our estimates of the current and future scrap-to-steel ratio across key regions is summarised in Figure 3 below.
Up to 2050 at least, there is simply not enough scrap to go around, with the global scrap-to-steel ratio likely to remain below 50% in the central case.
As a result, BF/BOF steelmaking, which relies on iron ore and metallurgical coal, will continue to be the dominant processing route for the manufacture of steel.
Even in our lower carbon case with an enhanced circular economy assumption driving higher scrap collection, the global BF/BOF share will still be over 50% by 2050.
Figure 3: historical and forecast global scrap to steel ratio by key regions. (Source: worldsteel, BHP analysis).
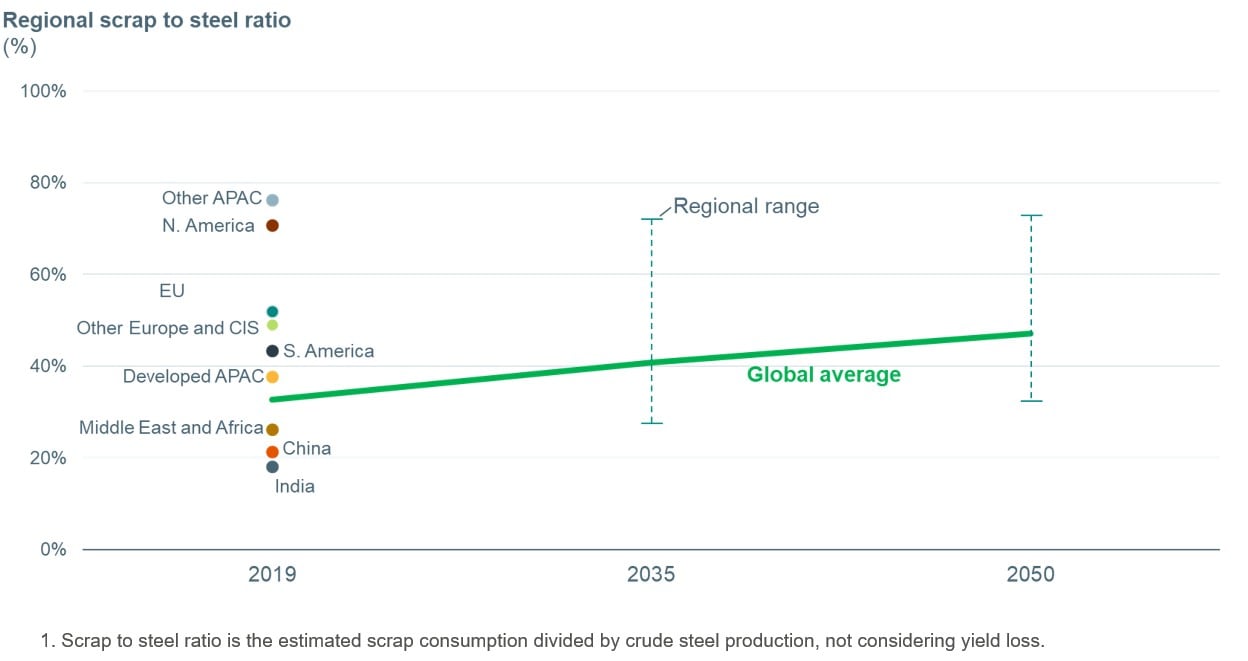
Similar to scrap, there is simply not enough high quality iron ore suitable for efficient DRI/EAF production to meet the global steel demand. With impurities such as silica, alumina and phosphorus strongly impacting the efficiency and competitiveness of the EAF process, DRI production must use the very highest quality iron ore, with an average iron content in the range of 67%. Such deposits are scarce. Without development in the DRI/EAF process that enables it to run efficiently with medium-to-high-grade ores, the very demanding feedstock requirement will limit its competitiveness.
How can the steel industry reduce emissions intensity?
Simply put, there are three options, all of which we expect to play a major role in decarbonisation:
- reduce or eliminate direct emissions at each steelmaking plant;
- reduce or eliminate carbon emissions through the use of renewable power; and/or
- capture carbon emissions for either re-use or storage.
Utilising our deep understanding of the steelmaking process, and the application of the Laws of Technological Diffusion that we have developed as a broader foresight tool, we have developed a proprietary Steel Decarbonisation Framework. This framework describes the stages that a steelmaking region must pass through on its decarbonisation journey, and outlines the technologies that are associated with each of them (Figure 4).
Figure 4: BHP’s steel decarbonisation framework.
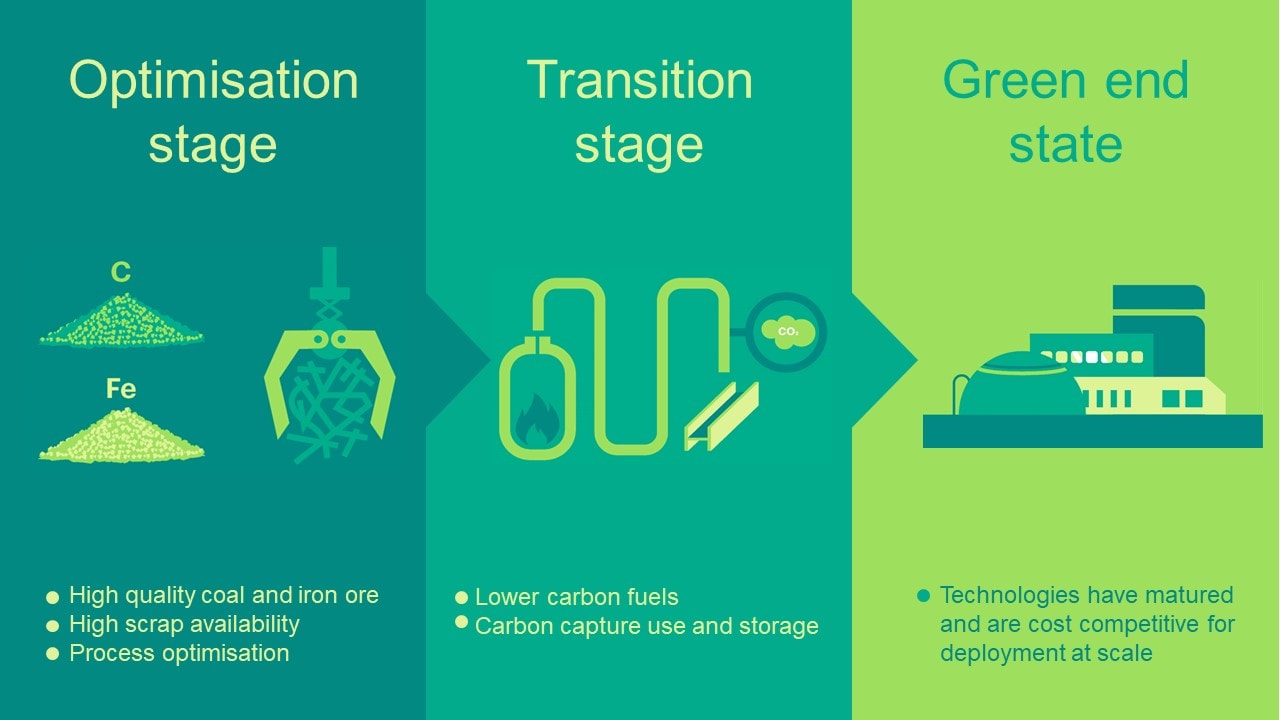
The three stages are Optimisation - where the majority of steelmaking regions sit today, followed by Transition and then ultimately, a Green end state.
Let’s take a closer look at the technologies and strategies within each stage.
Optimisation stage
As a first step, several low-cost abatement levers are available to reduce carbon emissions from the existing integrated steel making process. These include the use of renewable power, recycling of energy rich gases and heat. The implementation of advanced process control and Industry 4.0 will allow more steel producers to match the best-in-class performance achieved by the industry leaders. This will further reduce fuel usage and the related carbon emissions.
Higher quality raw materials like BHP's metallurgical coal and iron ore are another obvious avenue for emissions reduction. Higher iron content, lower impurity iron ore and higher strength coke made from premium hard coking coal, improves blast furnace efficiency and decreases emissions.
We expect scrap will also play an important role in the optimisation stage. Not only do we see the share of scrap-based EAF steel making increasing overtime, we also see some regions increasing their use of scrap within the integrated steelmaking process. Technically, scrap can be added to the BOF up to 30%, with the average roughly half that. We see this increasing over time. Even in the BF, (i.e. ironmaking) other metallics such as DRI/HBI, will play a role.
The most attractive optimisation opportunities for each steelmaking facility will differ based on the availability of cost competitive feedstock (ore-based raw materials and scrap), plant configuration and the final steel product mix. We believe the Optimisation stage has the potential to reduce carbon emissions intensity from the integrated steelmaking process by up to 20% from a baseline of 2.0 t CO2/t steel today.
Transition stage
This stage involves retrofitting existing integrated steelmaking facilities with low carbon technologies to deliver up to a 80% emissions intensity reduction, with more typical values in the range of 50%-60%. We see this stage playing a necessary role in making a material reduction to carbon emission in the medium term until the technology, economics and infrastructure required to support steelmaking in the Green end state viable. With many of these technologies increasing the efficiency of the blast furnace process, this reduces the potential to use off-gases for on-site power generation resulting in a need to import power from the grid. For this reason, access to renewable energy sources is required to realise the full potential of these technologies.
- Carbon capture utilisation and storage (CCUS) – We see CCUS playing a critical role in steel industry decarbonisation through the Transition stage. Depending on the configuration, CCUS has the potential to reduce emissions intensity of the integrated steelmaking process by up to 60%. While CCUS has not yet been deployed within the integrated steelmaking process due to several technical and economic challenges, we expect that these will be overcome in the coming decade. Carbon capture also has the benefit of being a technology that can be applied across sectors, such as stationary power generation, cement production and chemicals processing. Therefore, breakthroughs made in other sectors, and economies of scale from wider deployment across hard-to-abate sectors, may bring down costs for steelmakers. More information on the opportunities and challenges of CCUS can be found here.
- Oxygen blast furnace – This technology has the potential to bring about a positive step change for existing blast furnaces by injecting near pure oxygen into the furnace. The higher oxygen concentration coupled with a recirculating gas system (top gas recycling) has the potential to improve the efficiency of the blast furnace and lower overall emissions intensity by approximately 15%-20%. This technology was developed as part of the European ULCOS (Ultra-Low CO2 Steelmaking) project,3 as well as by world’s largest steelmaker China Baowu.4 One key feature is the high concentration of CO2 in the waste gas (~40 vs ~20% in the conventional blast furnace), which makes this technology an attractive option for pairing with CCUS.
- Smelting reduction – HIsarna, conceived under the ULCOS program and currently under development by Tata Steel Europe is one of the more promising technologies within this class.5 While this technology still uses coal as a reducing agent, it doesn’t rely on coke to provide the internal structure in the smelting vessel. The higher concentration of CO2 in the off gas (~90%) makes this technology well suited to combine with CCUS to reduce carbon emissions intensity by as much as 80%.
- Blast furnace hydrogen injection – This technology involves the injection of hydrogen through the tuyeres, either in the form of pure hydrogen or as hydrogen rich gases such as coke oven gas (approximately 55% hydrogen) or natural gas. Hydrogen injected through the tuyeres provides a source of heat and acts as a reducing agent to partially replace pulverised coal injected into the blast furnace. This technology is currently being trialled by leading steelmakers such as ArcelorMittal, China BaoWu and ThyssenKrupp Steel.6,7,8 While this technology shows promise, injection rates are limited due to the cooling effect hydrogen has inside the blast furnace, restricting the potential emission intensity reduction to around 15%. This technology is also being studied as part of Japan’s National COURSE50 (CO2 Ultimate Reduction in Steelmaking Process by Innovative Technology for Cool Earth 50) program.9
- Use of biomass – Biomass can be used across integrated steelmaking as a source of fuel or reductant, substituting coal or other fuels in the sintering process, as a blend component in the production of coke, as a direct replacement for coke or as an injectant to replace injected pulverised coal in the blast furnace, and as a source of carbon in the steelmaking process. When sourced from renewable resources, biomass has the potential to reduce emissions intensity by as much as 50% across the integrated steelmaking process. However, we believe 10%-20% is a more achievable objective. While biomass can play a small part in decarbonising the steel industry, we do not see biomass as a widespread abatement lever due to a lack of availability of sustainable sources of biomass and competing demand for what there is from other sectors.
Green end state
Finally, we see a Green end state where steel can be produced at or near zero emissions due to the adoption of transformative technologies. To achieve this, the industry will require access to renewable electricity that is cost competitive for deployment at scale to allow these technologies to compete, incentivising steelmakers to retire their existing blast furnace fleet. You can read our views on the decarbonisation of power here.
Currently, we see hydrogen based DRI/EAF steelmaking as the only plausible pathway to carbon free steelmaking that is deployable at scale. The use of hydrogen within the DRI process is not a new concept. Hydrogen makes up 60% of the reducing agent within the current natural gas based DRI processes. DRI facilities built today are also designed to be able to switch to hydrogen once it becomes available. The challenge is not so much a steelmaking technology challenge, but rather, the difficulties are related to the economics of supplying the vast quantities of renewable or green hydrogen to support the steel industry, including distribution and storage infrastructure.
To put the size of the challenge in perspective, a single 2 Mt per annum hydrogen based DRI plant requires an 800 megawatt electrolyser and the renewable energy supply equivalent of a small nuclear power station.
Not surprisingly, with the scale of supporting infrastructure, the economic challenges of hydrogen based DRI are enormous. Estimates suggest the cost to produce hydrogen would need around $1-2/kg in addition to a supportive carbon price environment to compete with the integrated steelmaking process. Nonetheless, interest in this technology is continuing to grow and the first hydrogen based DRI facility has just been commissioned in Sweden as part of the Hybrit project.10
Longer term we see emergent technologies such as direct iron electrolysis potentially playing a role. Today almost all primary aluminium and copper cathode is produced via electrochemical processes. The challenge for steel is to provide enough renewable electricity to produce steel at scale. For example, take Japan, which produces around 100 million tonnes of steel annually. To convert that level of output would require more than two times the total renewable electricity supply available today in the entire country. With that said, electrolysis offers the benefit of reducing iron ore directly with electricity, bypassing the need to produce hydrogen. For this reason, we believe electrolysis will continue to be developed as an alternative to hydrogen based steelmaking, should the economics of hydrogen never quite add up.
What is the outlook for steelmaking pathways over the next 30 years?
The next episode in our decarbonisation series will answer this question in some detail. For now, we note that the major steelmaking regions of China, Europe, India, and Japan are on different decarbonisation trajectories due to variations in domestic policy, their steel trade positions, the age of their blast furnace fleets, differential access to cheap renewable energy and varying demand for new capacity and affordable steel.
In conclusion, our research and our customer engagements both conclude that the blast furnace still has an important role to play in the future of steelmaking. With technology advancements, the blast furnace can still deliver significant and meaningful carbon emissions reductions while the economic and technology obstacles required for the Green end state are progressively removed. Our view is that despite the increase of scrap based EAF steelmaking and gradual shift towards the DRI route and other alternative technologies, the blast furnace route will still account for over half of steel production in 2050.
As a raw material supplier, BHP can play an important role in providing the high-quality raw materials required to support the steel industry as it moves through these three stages of decarbonisation. We will also partner with our customers. We expect to announce partnerships with leading steel manufacturers to develop and demonstrate technologies that will materially reduce carbon emissions from the steelmaking process. Stay tuned.
Footnotes
1 https://www.iea.org/reports/iron-and-steel-technology-roadmap
2 https://www.worldsteel.org/steel-by-topic/statistics/World-Steel-in-Figures.html
3 http://www.ulcos.org/en/index.php
4 http://www.bygt.com/nzcms_show_news.asp?id=6558
5 https://www.tatasteeleurope.com/static_files/Downloads/Corporate/About%20us/hisarna%20factsheet.pdf
6 https://corporate-media.arcelormittal.com/media/yw1gnzfo/climate-action-in-europe.pdf
7 http://www.baowugroup.com/#/aboutus/144/173?conid=999999999&artid=193860
8 https://www.thyssenkrupp.com/en/newsroom/press-releases/world-first-in-duisburg-as-nrw-economics-minister-pinkwart-launches-tests-at-thyssenkrupp-into-blast-furnace-use-of-hydrogen-17280.html
9 https://www.jisf.or.jp/course50/outline/index_en.html
10 https://www.hybritdevelopment.com/
Get the latest BHP news alerts, straight to your inbox
Get BHP news first. Stay in touch with our latest updates, investor news and media releases.