10 noviembre 2020
The first episode in our decarbonisation series looked at the critical enabler of achieving zero-carbon power generation. The second introduced our framework for assessing steel decarbonisation prospects, alongside a discussion of the current and emerging abatement levers the industry may deploy. This episode builds on that analysis to consider the most likely regional decarbonisation pathways. With China, Japan and South Korea all announcing national net zero ambitions in recent times, and Europe accelerating their longer-held ambitions, a regional narrative is particularly timely.
Our major conclusions are that:
- Decarbonisation pathways will reflect regional realities, and given very diverse starting points, the pathways are unlikely to converge on a single model for many decades.
- Aggressive policy and rapid advancement in general-purpose decarbonisation technologies are clearly required to induce higher-impact, higher-cost abatement levers across all regions.
- Notwithstanding the welcome uplift in regional decarbonisation ambitions we have seen of late, ‘hard-to-abate’ steel sectors in most regions face challenges to reach the green end state by 2050.
- An immense challenge awaits in developing regions such as India and Southeast Asia, where demand growth seems likely to heavily outweigh major prospective gains in efficiency.
Strong growth in steel demand in recent decades has seen absolute emissions from the sector increase, notwithstanding considerable achievements in the environmental profile of the global fleet and impressive gains in energy efficiency and carbon intensity (CO2 per tonne steel) dating back to the 1990s. First, the collapse of the Soviet Union saw a step change in steel emissions from the region. Second, the obsolete open-hearth furnace (OHF) has been largely phased out worldwide. Third, the modernisation of the Chinese steel industry - with new, state-of-the-art capacity and relentless environmental campaigns - has lowered the energy intensity per tonne of steel by more than 60% since 1990. Fourth, rising scrap availability in the developed world has also enabled a reduction in the carbon intensity of steelmaking in regions like the US and EU. And fifth, in Japan and South Korea, considerable technical efforts and increasing scale have moved the efficiency frontier of the blast furnace outwards.
The fact remains that the industry needs to redouble its efforts to achieve an end-state that aligns with the Paris accord and recent national level targets.
In a ‘business as usual’ (BAU) case , where demand growth is offset solely by ‘passive abatement’ opportunities that are available due to growing scrap supply and positive changes in the power mix, the global steel emissions baseline (absolute levels) will decline only marginally by 2050. While the emissions intensity per unit of steel will decrease noticeably, the industry would still fall far short of any desirable decarbonisation targets. This underscores the magnitude of the challenge that stands before the industry. Incrementalism will not win the day.
Figure 1 Global historical steel emissions and BAU case analysis in 2019-2050 (Mtpa CO2)
Sources: BHP analysis; worldsteel
Note:
- Steel output increase multiplying with initial base year emissions intensity.
- Include technological shifts, efficiency gains and passive abatement levers such as steel metallic and power mix changes from 1990 to 2019.
- Central-case scrap availability increase and business-as-usual natural-gas DRI development in gas-rich traditional markets.
Our steel decarbonisation framework highlights three distinct stages, beginning with the optimisation of existing technology and concluding with the green end state. Different types of abatement levers are adopted in each stage, with each region’s starting point in terms of indigenous fleet, infrastructure and feedstock availability a major influence on when these levers are likely to be pulled at scale. The highest impact levers from an emissions standpoint require progressively higher levels of policy support and very large investments in individual technology development, in addition to building out enabling ecosystems. Regional differences in these critical areas are at least as striking as the similarities. Accordingly, we anticipate that regional decarbonisation pathways will not easily converge in the coming decades with differentiation persisting for a considerable time to come, given variations in the following:
- Domestic policy favourability - Regional carbon taxes, levies or allowances, or emissions trading schemes (ETS), are important mechanisms to drive decarbonisation. A number of direct and indirect signposts indicate that regional differences in these policies are likely to be persistent. Given the importance of this lever to alter private sector behaviour, this will obviously lead to regionally specific rates of higher-cost technology take-up and different rates of progress through the phases.
- Alternative low-or-lower-carbon fuels availability – This is another unique local factor. Blast furnace steelmakers in natural-gas-rich North America are already injecting the lower-emissions fuel. The Middle-East steel sector is dominated by a gas-based direct reduced iron (DRI) process. In South America, biomass (charcoal) injection will continue to be a promising abatement lever.
- The age of blast furnace (BF) fleets – Steelmaking capital stock is long-lived, which is a double-edged sword where decarbonisation is concerned. Older facilities encourage steelmakers to jump to frontier technology. A newer facility makes retrofitting or modification more attractive. The average integrated plant age in the West is approaching 50 years, and local steelmakers therefore face relatively earlier decisions for technological switching. By contrast, the BF fleet in China is only about 12 years old, while India (average age is around 18 years with more new furnaces underway) and Southeast Asia (even newer than China) have similarly young fleets. Therefore, in populous emerging Asia, transitional abatement levers such BF modification and carbon capture, utilisation and storage (CCUS) are very realistic options.
- Divergent demand for new capacity – Regional steel demand trajectories determine ‘emissions baselines’ in absolute terms. Steel emissions in most developed regions are expected to continue to decline. China will soon follow suit. However, steel demand is still growing in other developing regions. Collectively, they are expected to be the main source of growth in regional steel emissions.
- Different steel net trade positions – Steel is a globally traded commodity. While wealthy regions with marginal imports dependency are mulling ‘green border taxes’, some developing regions heavily rely on cheap steel imports to contain building costs for much needed infrastructure and housing. Meanwhile export-oriented steelmakers have to carefully balance their cost-competiveness and decarbonisation ambitions.
(Note that we do not include scrap availability and renewable power in this list, despite their great influence on regional decision making, as we class them as ‘passive levers’ embedded in the simple BAU case).
Before we dive into details of the cases we are going to discuss, it is useful to emphasise that the difference between the cases is not the amount of steel demanded: it is how that demand is met. The emissions range therefore reflects the policy and technological uncertainty inherent in any long-term simulation, but not end-use demand uncertainty. This approach is consistent with the method we apply to our integrated energy system and climate scenarios, where the same amount of final energy services are delivered in each. It is just that they become progressively more efficient in terms of primary energy and emissions intensity as they move to the green end of the policy, behaviour and technology spectrum.
In the pathway that accords with the power mix and carbon pricing assumptions embodied in the Central Energy View documented in our Climate Change report (CCR), absolute global steel emissions are likely to decline by a little less than 15% from 2019 to 2050. In this central case, the majority of steelmakers are expected to focus on process optimisation. Leading steelmakers in some regions will continue to trial and eventually adopt more costly abatement technologies, consistent with the announced objectives of a number of European producers.
In the lower carbon case, also documented in the CCR, worldwide steel emissions could fall by more than twice as much as in the Central case. A more supportive policy environment, including higher carbon prices, could foster the circular economy (higher-than-base-case scrap collection) as well as providing enhanced Scope 2 abatement opportunities for steelmakers via a swifter decarbonisation of the power mix. These conditions are likely to incentivise wider adoption of high-cost abatement levers, such as CCUS and hydrogen steelmaking. The global outcome in this case (about -30% versus BAU) hides considerable regional variation. The EU leads the technological decarbonisation effort, while emerging regions achieve a relatively smaller saving against their 2050 BAU baseline emissions. A sense of that complexity comes through in Figure 2 below. This chart also shows the bottom-up techniques we use as a basis of all our longer-term analysis.
Figure 2 Global steel emissions pathways and 2050 regional abatement by levers in lower carbon case
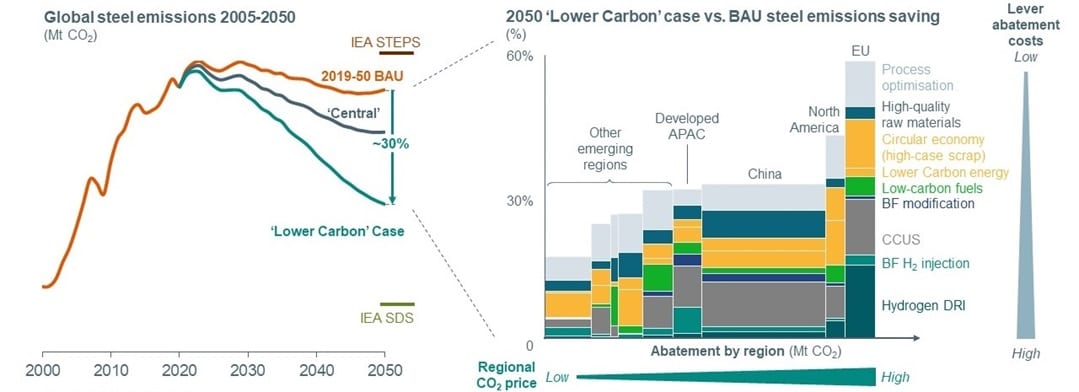
Source: BHP analysis; IEA.
Note: BHP Central Energy View (Central case) tracks 3◦C temperature increase above pre-industrial level. BHP Lower Carbon View tracks approximately 2.5◦C increase. IEA State Policies Scenario (STEPS) is the baseline scenario in its Iron and Steel Technology Roadmap 2020. The IEA Sustainable Development Scenario (SDS) tracks 1.5~1.65◦C temperature rise.
Our central and lower carbon cases sit comfortably between the two “book-end” scenarios from the International Energy Agency (IEA) included in Figure 2. The IEA STEPS is comparable to our BAU case in spirit. The IEA’s Sustainable Development Scenario (SDS) works towards a global temperature outcome of 1.5 to 1.65 degrees Celsius above pre-industrial levels, which requires deep and early decarbonisation across all sectors as well as a massive roll-out of negative emissions technologies. It is not directly comparable to our lower-carbon case, partly due to the fact it assumes that fewer tonnes of steel will be needed as a result of progress in ‘materials efficiency’. It also introduces a novel leap-frogging assumption for India, which we consider in the regional discussion below.
We will now examine four major steelmaking regions - China, Developed Asia-Pacific, Europe, and India - in turn.
Figure 3 Steel emissions for key regions (Mtpa CO2)
Source: BHP analysis
China (53% of global steel production in 2019, 1.8 t C02 intensity per tonne)
China is estimated to contribute more than 60% of global steel emissions today. With Chinese steel production entering its plateau phase in the next decade, and scrap availability rising strongly, passive abatement in China stands to make a major contribution to absolute emission reduction in the coming decades. We put China’s passive abatement opportunity at about two-fifths of the 2019 level: which is easily the largest absolute emissions decline among all steelmaking regions.
Even so, China could do more in steel decarbonisation: and given what we think about likely trends in lower income markets like India (see below), it will need to.
Chinese blast furnaces (BF), with their operational agility, have been taking most of the low-Fe-content iron ore available in the seaborne market. This starting point represents an optimisation opportunity to blend with higher-grade ores to cut emissions. In addition, continuous technological upgrades to meet stringent environmental standards could also drive emissions down further.
Premium quality seaborne hard coking coals are already highly prized by integrated mills on the coast for their productivity benefits. The commercial efficiency imperative of today will increasingly extend to the emissions advantages that these coals offer.
China’s progression into the Transition Stage will require sponsorship from supportive policies, notably with the introduction and then maturation of an emissions trading scheme. Rising effective carbon prices are required to incentivise higher-cost and higher-effect abatement levers. China has one of the youngest BF fleets. More than half of China’s existing BF capacity of around 1 billion tonnes will still be in robust operational shape in 2050. Economies of scale are also likely to remain a durable feature of the competitive landscape in China’s domestic mega market. However, by this stage many will have been adapted to inject low-carbon fuels – such as biomass and hydrogen. Moreover, relatively new facilities and competitive construction costs could make CCUS a viable solution. A BHP sponsored study by University of Edinburgh surveyed 17 integrated steel plants in China, and judged that 13 of them were suitable for retrofitting with amine separation technologies for carbon capture. Seven of the 13 also saw storage opportunities for enhanced oil recovery (EOR) to reduce the net CCUS cost further.
In the lower carbon case to 2050, Chinese steel emissions could fall by more than -60% from the 2019 level. We estimate CCUS will play a much bigger role in Chinese emissions abatement than hydrogen direct reduced iron (DRI) in the coming decades.
China has never established a traditional DRI market, and its immense store of metallurgical knowledge and engineering experience have been tied up in the BF/BOF process. Where Chinese steelmakers do edge in the direction of hydrogen, they seem best placed to use hydrogen produced from coke oven gas for DRI pilot projects in advance of a much longer-dated and gradual transition towards green-hydrogen-based reduction.
European Union (8% of global steel production in 2019, 1.3 t C02 intensity per tonne)
Over the past three decades, EU steel emissions have declined by about one-third in absolute terms due to lower demand and capacity closures. This downward trend is likely to continue; the major driver is this new era will be technology rather than demand. The EU presently produces almost 60% of its steel via the BF/BOF route. As the world’s biggest net exporter of ferrous scrap, the region could use more local scrap as the first step to cut its carbon footprint. Several EU BF steelmakers have been mulling a shift to the scrap-based EAF route in their recent revitalisation plans. This, alongside the rising penetration and falling cost of renewable power, could drive EU ‘baseline’ steel emissions intensity in 2050 close to the current North American levels, where the scrap-to-steel ratio is almost 20 percentage points higher than in the EU today.
The EU has long been a very ambitious decarboniser. EU steelmakers are willing to experiment with multiple abatement levers for emissions reduction, and leading European steelmakers have recently unveiled ambitious roadmaps to future carbon neutrality. EU mills, in general, consume high-quality raw materials and bring world-class technical and operational know-how: but their facilities are aging. Many facilities date back to the reconstruction boom of the 1950s and 1960s, and the majority were in place by the end of the 1980s. All else equal, the older the facility, the less attractive are the economics of retrofitting. That is the reverse of the Chinese situation. What an older fleet does do is increase the appetite in the EU for investing in emerging technologies. This has sparked a lot of experimentation and innovation. The EU steelmakers operating some of world’s oldest integrated facilities are now leading the development and commercialisation of hydrogen-based DRI. Before the early stage commercialisation of hydrogen DRI (likely in the late 2030s), we believe a wide range of abatement levers will be adopted in the EU. These range from injecting alternative BF fuels (e.g. biomass and recycled materials); to CCUS being added to blast furnaces and smelting reduction facilities. These could all make a significant contribution to the region’s steel decarbonisation in the next three decades.
In our lower carbon case, EU emissions intensity could fall to a strikingly low level of 0.3 to 0.4 t CO2/ t steel by 2050, lowering its annual steel greenhouse emissions by more than -70% from today.
That is a level in line with the low carbon roadmap laid out by European Steel Association (EUROFER). Achieving the lower carbon case for the entire EU steel sector would lower absolute global steel emissions by about -5%.
Developed Asia-Pacific (11% global steel production in 2019, 1.5 C02 intensity per tonne)
Developed Asian steelmakers have been the global champions in the development and adoption of energy saving technologies. As they currently represent the frontier of efficiency in the BF, low-cost abatement options are limited for Japanese and South Korean steelmakers. However, there is still some room to optimise with higher quality raw materials in both iron ore and metallurgical coal, noting that Japan’s coal procurement strategies are in the middle of the quality spectrum. Better raw material quality and coke battery refurbishment could result in lower fuel rates.
Among the major steelmaking regions, Japanese and Korean mills have very high exposure to direct and indirect steel exports, and they need to continue to compete effectively internationally in the face of shrinking domestic demand over the long-term. Local steelmakers have set out to pursue a pragmatic decarbonisation route. This is embodied in COURSE 50, a Japanese developed low-carbon BF technological roadmap, with phased technological upgrades and retrofits of existing blast furnaces taking coke oven syngas or low-hydrogen injection.
As a major steel-exporter, the likelihood of green tariffs or border adjustments being imposed at home to support more aggressive decarbonisation is relatively low.
In a more aggressive transitional paradigm, COURSE 50 BFs have the potential to upgrade their abatement capability in combination with CCUS, which could significant lower the steel industry’s environmental footprint.
The end-of-the-pipe solution could also be applied to local smelting reduction, where Korean steelmakers have a technological edge. We don’t see Northeast Asia as a favourable region for hydrogen DRI due to fact that affordable electricity is, and will continue to remain, a challenging proposition. Additionally, as the region has long been dominated by BF-BOF steelmaking, it lacks experience in DRI technologies, similar to China.
India (6% global steel production in 2019, 2.4 C02 intensity per tonne)
India’s steel emissions intensity is now among the highest in the world. It relies heavily on blast furnaces and coal-based DRI. In 2019, Indian primary iron production almost equated with crude steel output, implying very low scrap usage. Over the coming decades, India’s urbanisation and industrialisation are expected to bring huge demands for affordable steel. Bigger-sized modern BF-BOF plants are likely to take share away from emissions-intensive coal-based DRI and obsolete induction furnace units. While BF performance optimisation is likely to achieve a -10% emissions reduction with higher energy efficiency, stronger coke and higher pulverised coal injection (PCI) injection rates will keep overall emissions intensity substantially higher than other major steelmaking regions.
In a BAU analysis, India, along with other emerging regions like South-east Asia, Middle East and Africa, will contribute more to steel emissions than China by 2050. This underscores the fact that developing economies such as India face arguably the sternest decarbonisation challenge.
To precipitate a more aggressive push for decarbonisation, we would need to see disruptive changes to India’s environmental policies. That would require an alteration of societal priorities in a nation that still faces many basic economic development challenges. In steel itself, land acquisition laws and approval permit regulations will need to become more flexible and pro-business to facilitate industrial growth on the scale required. This is not to say that none of the mid-to-high-cost abatement levers will be triggered in India. The operational presence of multinational steelmakers in India offers some hope in this regard. These firms can deploy what they learn in other jurisdictions to their Indian operations. There are clear potential gains in BF optimisation for a start. Still, even in our lower carbon case, Indian steel emissions in 2050 could be more than double its current level, despite a steady decline in carbon intensity per tonne of steel.
The IEA’s Sustainable Development Scenario (SDS) argues that India could ‘leapfrog’ to hydrogen-based steelmaking alongside a wide adoption of CCUS on blast furnaces and innovative smelting reduction. We certainly see India’s current fleet of coal-based DRI, which is a unique outgrowth of India’s local endowments (good iron ore resources, a lack of scrap, a lack of met coal and an abundance of cheap thermal coal) as ready for positive disruption by either conventional or emergent technology. There are unfortunately a number of impediments to the broader optimistic vision. A lack of renewable power infrastructure to make electrification green is an issue. So is the low level of scrap availability and modest industrial capability as a whole, plus the enormous amount of capital that needs to be mobilised to improve investment on each front. As our technological diffusion framework makes clear, fundamentally transforming a sector with a long-lived incumbent capital stock as well as economy-wide infrastructure requirements that are not yet in place, takes concentrated effort over a very long time. This is not like switching to smart phones or adopting ride hailing.
This is not like switching to smart phones or adopting ride hailing.
In conclusion, each of the four major regions we have surveyed has a potential pathway to a significantly improved decarbonisation performance on an intensity basis: and three of the four are also likely to achieve significant cuts in absolute emissions. However, only Europe seems likely to be approaching the pure green end state by 2050. China and developed Asia-Pacific are more likely to be in mid-to-late transition with massive rollout of CCUS and modified BFs for lower-carbon injection substitutes. India is more likely to be somewhere between late optimisation and early transition. A more ambitious outcome would depend on both very supportive policy changes in India and a significant injection of technology from other regions.
Footnotes
1. Estimated steel-making direct emissions from ironmaking (including captive sintering, pelletising and coking), steelmaking, casting and hot rolling and electricity purchased for the processes.
2.The estimated average age of integrated plants since the start of operation is based on a sample of capacity, not a census of the fleet. The ‘furnace age’ would be shorter as blast furnaces tend to be relined every 15-20 years.
3. The carbon intensity is calculated with direct emissions from ironmaking, steelmaking, casting and hot-rolling and indirect emissions from purchased electricity, scaled by crude steel output
4. The exact impact on global emissions if this occurred is not clear. It is possible that if a shortage of traded scrap emerged due to a decline in EU exports, new BF/BOF capacity could be induced in former scrap importing regions. The net impact would therefore be the gap between the carbon intensity of the displaced capacity in the EU and the new capacity in, say, Turkey.
5. Alternative pathways’ with low-CO2 energy scenario in Low Carbon Roadmap by EUROFER in November 2019